Nachrichten
Wie kann man die schädlichen Auswirkungen von Lärm auf Lager vermeiden?
2024-11-27Rillenkugellager sind als wichtige Komponente in mechanischen Systemen weit verbreitet und werden in verschiedenen Industrieanlagen, Transportfahrzeugen und Haushaltsgeräten eingesetzt. Allerdings ist das Geräusch von Rillenkugellagern oft ein großes Problem, das die Leistung der Geräte, die Betriebsstabilität und die Benutzererfahrung beeinträchtigt. Eine eingehende Analyse hilft dabei, die Ursache des Geräusches genau zu identifizieren, um wirksame Lösungen zu finden und den normalen und effizienten Betrieb der Geräte sicherzustellen.
Ursachen von Geräuschen bei Rillenkugellagern
1. Fehler während der Herstellung
Die Oberflächenrauheit der Wälzkörper entspricht nicht dem Standard: Wenn die Schleif- und Poliertechniken für Wälzkörper während der Bearbeitung nicht perfekt sind, kommt es zu leichten Unregelmäßigkeiten auf ihren Oberflächen. Wenn sich das Lager dreht, ist der Kontakt zwischen den Wälzkörpern und den inneren und äußeren Laufbahnen nicht mehr ideal glatt. Dieser unregelmäßige Kontakt löst hochfrequente Vibrationen aus und erzeugt scharfe Geräusche.
Rundheitsfehler der inneren und äußeren Laufbahnen: Der Verschleiß der Fertigungsformen und die unzureichende Präzision der Verarbeitungsgeräte können dazu führen, dass die Rundheit der inneren und äußeren Laufbahnen von den Konstruktionsstandards abweicht. Wenn die Wälzkörper in den Laufbahnen rollen, ist die von ihnen getragene Kraft ungleichmäßig. Die periodischen Kraftänderungen veranlassen das Rillenkugellager, Vibrationsgeräusche zu erzeugen, wobei die Geräuschfrequenz in der Regel mit der Drehfrequenz des Lagers zusammenhängt.
2. Unsachgemäße Montage
Unangemessene Vorspannung: Die übermäßige Vorspannung erhöht die Reibung zwischen den verschiedenen Komponenten im Lager erheblich, was nicht nur den Verschleiß beschleunigt, sondern auch aufgrund der übermäßigen Kompression zu kontinuierlichen Reibungsgeräuschen führt. Andererseits kann unzureichende Vorspannung die Steifigkeit des Lagers nicht gewährleisten, wodurch die Wälzkörper während des Betriebs anfällig für Erschütterungen sind und mit den Laufbahnen kollidieren, was zu Geräuschen führt.
Exzentrische Montage: Wenn das Lager mit einer gewissen Exzentrizität auf der Welle oder in der Gehäusebohrung montiert wird, wirken bei der Drehung zusätzliche radiale oder axiale Kräfte auf das Rillenkugellager, was zu ungleichmäßigen Kräften auf die Wälzkörper führt, unausgeglichene Vibrationen auslöst und somit Geräusche erzeugt. Diese Geräusche weisen in der Regel offensichtliche periodische Merkmale auf.
3. Schlechte Schmierung
Unzureichende Schmierung: Wenn das Lager mit hoher Geschwindigkeit läuft, ist ausreichend Schmiermittel zwischen den Wälzkörpern und den Laufbahnen erforderlich, um einen Ölfilm zu bilden und die Reibung zu verringern. Wenn die Schmiermittelmenge nicht ausreicht, kommt es zum verstärkten direkten Metall-auf-Metall-Kontakt, der Reibungskoeffizient steigt an und es entstehen Trockenreibungsgeräusche, die sich typischerweise als scharfe „Quietschgeräusche“ äußern.
Verunreinigtes Schmiermittel: Verunreinigungen wie Staub und Metallabrieb in der Arbeitsumgebung vermischen sich mit dem Schmiermittel, wodurch die Integrität des Ölfilms beschädigt und die Schmierwirkung stark verringert wird. Diese Verunreinigungen können auch als abrasive Partikel zwischen den Wälzkörpern und den Laufbahnen wirken, was den Verschleiß verschlimmert und zusätzliche Geräusche erzeugt. Die Geräusche weisen oft unregelmäßige Schwankungseigenschaften auf.
4. Unnormale Belastungen
Überlastung: Wenn die tatsächliche Belastung der Ausrüstung die vorgesehene Tragfähigkeit des Rillenkugellagers übersteigt, steht jeder Teil des Rillenkugellagers unter übermäßigem Druck, neigt zu plastischer Verformung und der Kontaktzustand zwischen den Wälzkörpern und den Laufbahnen verschlechtert sich, was zu starken Vibrationsgeräuschen führt. In schweren Fällen kann es sogar zum vorzeitigen Lagerausfall kommen.
Stoßbelastungen: Bei einigen Geräten mit intermittierenden Arbeitseigenschaften, wie Stanzmaschinen und Brechern, üben häufige Stoßbelastungen augenblicklich enorme Kräfte auf die Lager aus, wodurch die innere Struktur der Lager beeinträchtigt und in Schwingung versetzt wird, was zu augenblicklichen Geräuschen hoher Intensität führt. Unter solchen Arbeitsbedingungen wird die Lebensdauer des Lagers bei längerer Dauer erheblich verkürzt.
5. Verschleiß und Ermüdung der Lager
Normaler Verschleiß: Bei der Verwendung des Lagers im Laufe der Zeit verschleißen Komponenten wie Wälzkörper, Innenring und Außenring allmählich, die Laufbahnoberflächen werden rau und die Abstände vergrößern sich. Zu diesem Zeitpunkt werden während des Betriebs Geräusche erzeugt, die auf die abnehmende Passgenauigkeit zwischen den Komponenten zurückzuführen sind. Im Allgemeinen nehmen die Geräusche allmählich zu, wenn der Verschleißgrad zunimmt, und der Ton neigt dazu, dumpf zu werden. Nachdem das Oberflächenmaterial des Lagers über einen längeren Zeitraum der Wechselbelastung ausgesetzt war, treten Ermüdungserscheinungen auf, wobei winzige Abplatzungen entstehen. Diese Abplatzungen stören die Gleichmäßigkeit des Wälzkontakts, lösen periodische Stoßvibrationen aus und erzeugen Geräusche mit offensichtlichen Impulscharakteristiken, was in der Regel darauf hindeutet, dass das Rillenkugellager kurz vor dem Versagen steht.
Maßnahmen zur Lösung von Lagergeräuschproblemen
1. Optimierung der Fertigung
Verwendung von hochpräzisen Verarbeitungsgeräten und fortschrittlichen Schleif- und Poliertechniken, strenge Kontrolle über Oberflächenrauheit von Wälzkörpern und Laufbahnen und Sicherstellung, dass die Bearbeitungsgenauigkeit den Konstruktionsanforderungen entspricht, wodurch Geräusche, die durch Fertigungsfehler verursacht werden, an der Quelle reduziert werden. Regelmäßige Inspektion und Wartung der Fertigungsformen, um die Rundheitsgenauigkeit der inneren und äußeren Laufbahnen zu gewährleisten und gleichzeitig die Kontrolle über Rohstoffqualität zu verstärken, um die Gesamtfertigungsqualität der Lager zu verbessern.
2. Standardisierung des Montage
Je nach Art, Größe und Einsatzbedingungen der Rillenkugellager ist die geeignete Vorspannung genau zu berechnen und anzuwenden. Zur Erkennung können professionelle Vorspannungsmessgeräte eingesetzt werden, um die Genauigkeit der Installation zu gewährleisten.
Verwenden Sie beim Einbau von Lagern hochpräzise Montagewerkzeuge und Positionierungsvorrichtungen, um die Exzentrizität beim Einbau streng zu kontrollieren und die Koaxialität des Lagers mit der Welle und der Gehäusebohrung sicherzustellen. So werden die durch unsachgemäße Montage verursachten zusätzlichen Kräfte und Vibrationen reduziert.
3. Stärkung des Schmiermanagements
Bestimmen Sie die Art, Qualität und Füllmenge der Schmiermittel entsprechend den Arbeitsanforderungen der Rillenkugellager, richten Sie ein regelmäßiges Schmierwartungssystem ein und füllen Sie die Schmiermittel rechtzeitig nach, damit die Lager in einem guten Schmierzustand arbeiten.
Ergreifen Sie wirksame Dichtungsmaßnahmen, um zu verhindern, dass Verunreinigungen von außen in das Innere der Rillenkugellager gelangen, und reinigen oder ersetzen Sie die Schmiermittel regelmäßig, um die Reinheit der Schmiermittel zu gewährleisten und gute Schmierwirkung zu erhalten.
4. Lasten angemessen kontrollieren
Bewerten Sie während der Konstruktionsphase der Ausrüstung die Arbeitslast genau, wählen Sie Lager mit geeigneten Tragfähigkeiten aus und halten Sie eine gewisse Sicherheitsmarge ein, um die Überlastung der Lager zu vermeiden.
Bei Geräten mit Stoßbelastungen sollten Puffer wie Federn und Gummipuffer eingebaut werden, um die Stoßbelastung der Lager zu verringern. Gleichzeitig sollte der Arbeitsprozess der Geräte optimiert werden, um die Häufigkeit und Intensität von Stößen zu verringern.
5. Regelmäßige Überwachung und Wartung
Einrichtung eines Überwachungssystems für den Betriebszustand der Lager, Erfassung von Echtzeit-Betriebsdaten der Rillenkugellager über Geräte wie Vibrationssensoren und akustische Sensoren und Einsatz von Datenanalyseverfahren, um Verschleiß, Ermüdung und andere abnormale Zustände der Lager frühzeitig zu erkennen, Frühwarnungen auszugeben und entsprechende Wartungsmaßnahmen zu ergreifen. Entwickeln Sie einen regelmäßigen Wartungsplan, demzufolge verschlissene Teile der Lager regelmäßig demontiert, inspiziert, gereinigt und ausgetauscht werden. Beseitigen Sie potenzielle Fehlerquellen rechtzeitig, damit die Lebensdauer der Lager verlängert und die Möglichkeit der Geräuschentwicklung reduziert wird.
Für weitere Informationen wenden Sie sich bitte an QIBR
Weitere Artikel
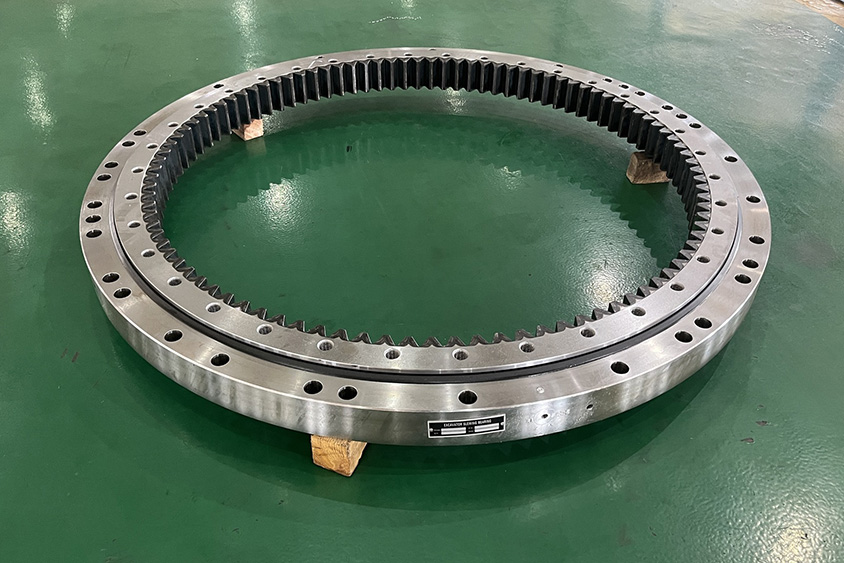
Einführung in das Spiel von Drehverbindungen

Warum können Drehverbindungen nicht mit hoher Geschwindigkeit rotieren?
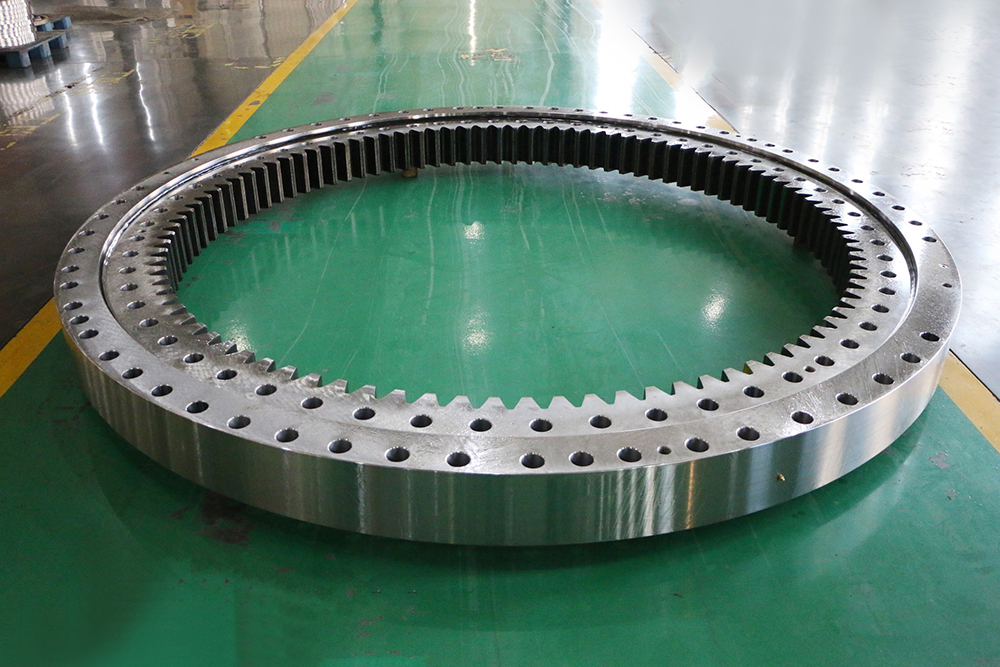
Was ist der Unterschied zwischen einem Drehverbindung und einem Wälzlager?
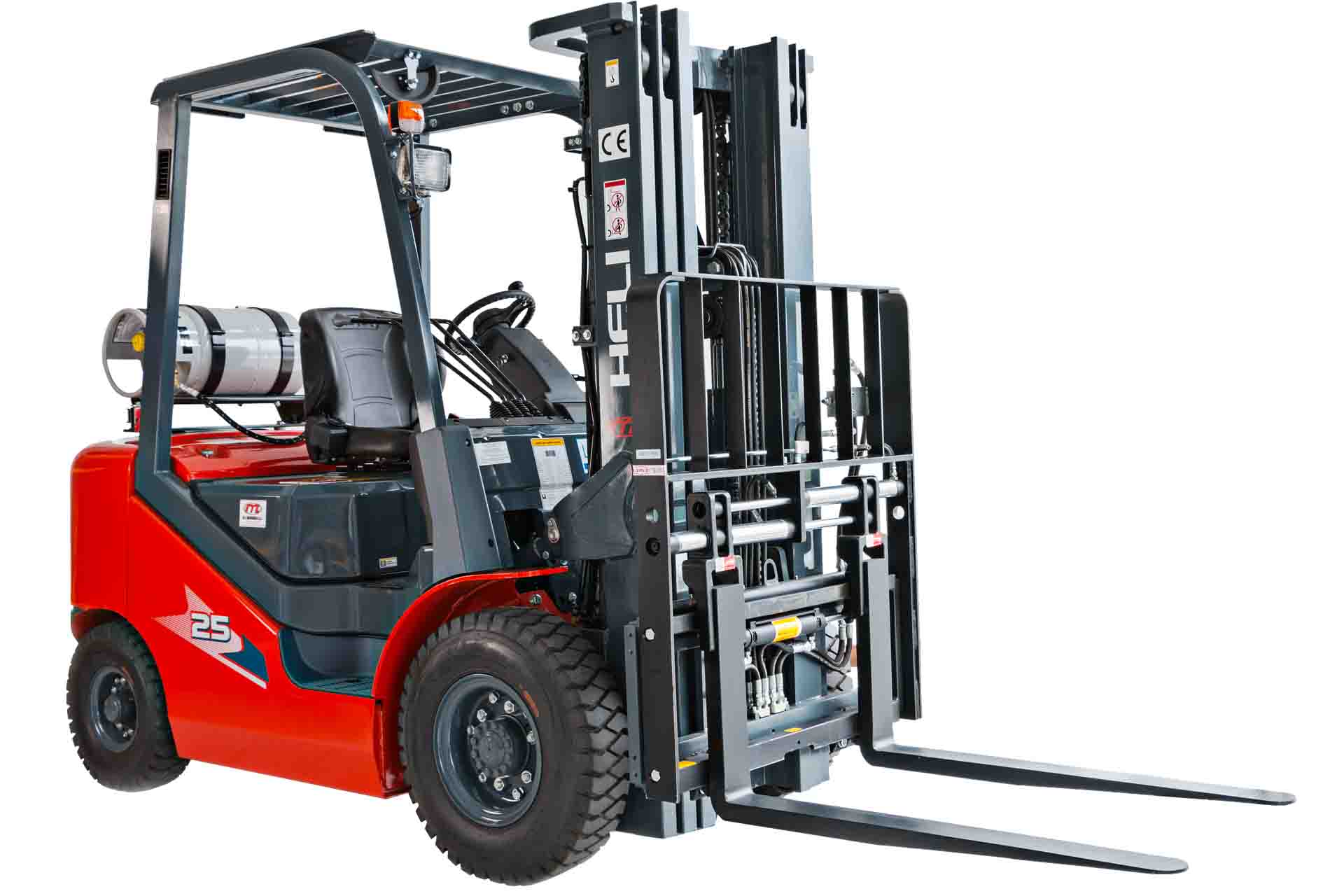
Was ist der Drehkranz des Gabelstaplers?
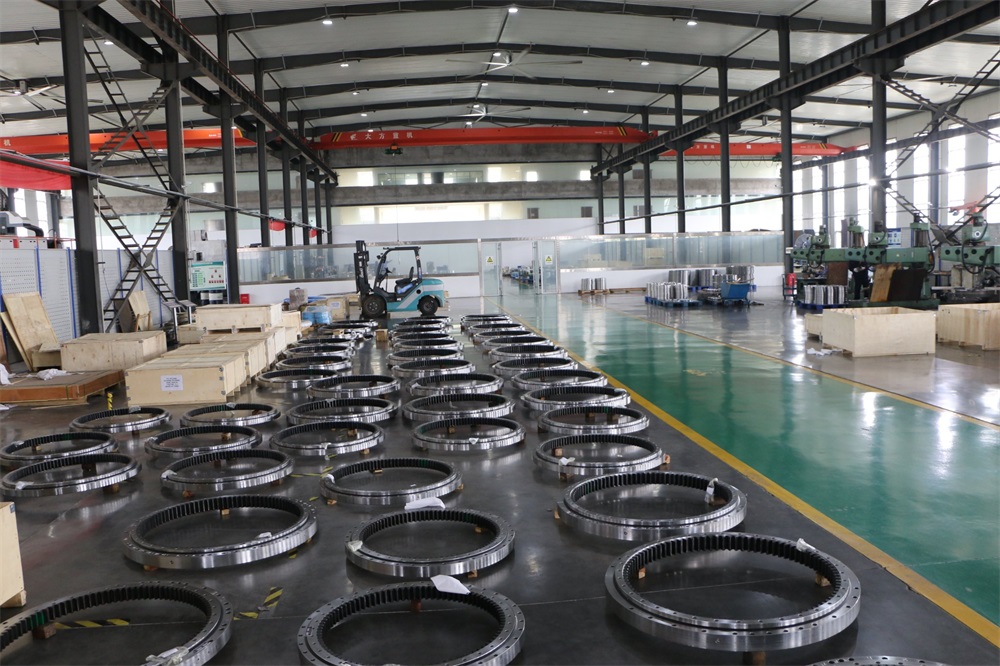